The Advanced Low Cost Aircraft Structures (ALCAS) project, led by Airbus, sought to reduce both the weight and cost of airliner wings. Jody Muelaner was the Technical Lead for Metrology on this project.
Interface Management
A key area of interest was the interface between the wing box ribs and the upper cover. The cover was produced using a resin infusion moulding technique. This produces the panel structure on a single sided mould with the outer aerodynamic profile tightly controlled, this is known as the outer mould line (OML). The inner profile which must interface with the spars and ribs is formed using a vacuum bag and is therefore not tightly controlled, this surface is known as the inner mould line (IML).
Jody supported the development by Airbus in the UK of a process to machine the wing box ribs during assembly to fit to the uncontrolled cover IML. This required accurate measurements of the cover IML to be made and for a flexible industrial robot to datum its-self and machine the rib feet with respect to these measurements.
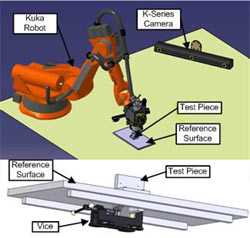
Uncertainty Modelling
The first phase of the work carried out was to model the uncertainty of the complete process in order to provide advice on process optimization and predicted capability. Jody was involved in developing innovative techniques for the modelling of metrology enabled processes, these were deployed in the modelling of this process. These techniques model the combined uncertainty of a complete process combining process variability with measurement uncertainty. Analytical uncertainty evaluation and Monte Carlo simulation are used to propagate these components of uncertainty to determine the combined process uncertainty.
