Customer Profile and Brief
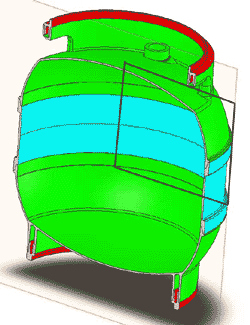
CypherCo are a manufacturer of specialist fluid transfer products for the beverage and agro-chemical industries world-wide. I was contracted to determine cause of failure on a moulded plastic cask under a 1 Bar internal pressure loading.
Problem Solution
Stresses acting on the barrel under an internal pressure loading were investigated using both finite element and classical analysis. I greatly simplified the supplied geometry to create a highly efficient axisymmetric finite element model allowing a very robust solution.
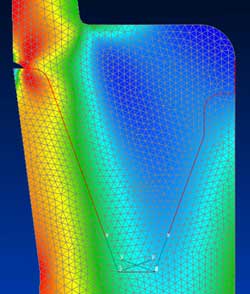
A convergence study was carried out on the maximum stress and total vertical deflection. This established the degree of mesh refinement required for accurate results and showed that stress results were accurate to within 5%. Coordinate systems were created on the weld lines so that normal and shear stress could be examined for each weld surface individually.
Cause of Failure
It was found that failure at the weld was most likely due to a combination of:-
- A stress concentration in the surrounding geometry leading to peak
stresses at the inner edge of the weld. - Further stress concentration at the weld edge due to the weld line
its-self acting as a crack type stress raiser. - Possibly also an imperfect weld leading to less than full material
strength in this region. - Classical analysis was used to determine the actual stress due to the
weld line acting as a stress raiser.
Leave a Reply