This paper presents a complete framework for achieving part-to-part assembly though the use of measurement assisted assembly. It starts by setting out the objectives for low cost and high quality aero structure assembly. These objectives include achieving part-to-part assembly, low cost flexible automation and tooling, traceable quality assurance and control, reduced structure weight and improved aerodynamic tolerances.
It explains why challenges encountered in industries such as aircraft and spacecraft production mean that traditional approaches such as interchangeability are not cost effective at bringing about part-to-part assembly or improving structure tolerances. The alternative methods possible using measurement assisted assembly are shown to be more suitable in these industries. A complete digital architecture for the efficient implementation of measurement assisted assembly is shown in detail and the further development of measurement assisted assembly is presented as a roadmap to part-to-part assembly.
Part-to-part Assembly Paper Details
Title: Achieving Low Cost and High Quality Aero Structure Assembly through Integrated Digital Metrology Systems
By J E Muelaner, O C Martin, P G Maropoulos
Presented at the Forty Sixth CIRP Conference on Manufacturing Systems 2013 (CMS2013) in Portugal
Published in: Procedia CIRP, Volume 7, 2013, Pages 688–693
Abstract: Measurement assisted assembly (MAA) has the potential to facilitate a step change in assembly efficiency for large structures such as airframes through the reduction of rework, manually intensive processes and expensive monolithic assembly tooling. It is shown how MAA can enable rapid part-to-part assembly, increased use of flexible automation, traceable quality assurance and control, reduced structure weight and improved aerodynamic tolerances. These advances will require the development of automated networks of measurement instruments; model based thermal compensation, the automatic integration of ‘live’ measurement data into variation simulation and algorithms to generate cutting paths for predictive shimming and drilling processes. This paper sets out an architecture for digital systems which will enable this integrated approach to variation management.
Official URL: http://authors.elsevier.com/sd/article/S2212827113003235
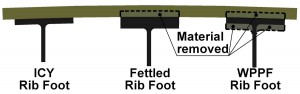
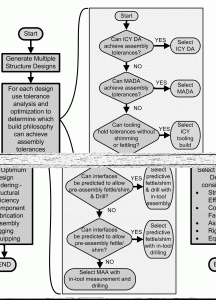
Leave a Reply